Design Features Bearing:
This Bearing offers dependable and efficient performance in industrial applications where space is at a premium. It characters high-speed capabilities, low friction, and minimal noise levels, ensuring optimal performance. Built to meet industry standards for precision and durability, it is an ideal choice for a variety of compact-space applications in diverse industries.
Applications Bearing:
This Bearing finds applications in various industries that require high precision and compact design, such as medical devices, robotics, and aerospace technology. It is also used in computer hard drives, motors, and instrumentation equipment. Its small size and efficient performance make it a popular choice for industries where space is limited but high precision is essential.
Maintenance and Troubleshooting Tips of Bearing:
To ensure optimal performance and longevity of Bearing, regular maintenance is necessary. Inspect the bearing frequently for any signs of damage, wear, or contamination. Clean it with a non-corrosive solvent and dry it thoroughly before lubrication. If any damage or excessive wear is detected, replace the bearing immediately. In case of any issues with the application, troubleshoot to ensure the bearing is being used within its designed parameters.
Characteristics and uses of miniature ball bearings
Bearings with an inner diameter less than 10mm or an outer diameter less than 28mm are usually called miniature bearings. Mainly used in instrumentation and medical equipment.
Its characteristics are:
1. The miniature bearings used in synchronous motors and servo motors are mainly radial ball bearings with dust covers, which often require supplementary friction torque. They are easy to start and run smoothly.
2. In order to meet the high-precision and high-speed operation requirements of gyromotors, high-precision radial thrust ball bearings or radial thrust ball bearings with thrust ribs are often used. The latter can simplify installation and reduce errors. There are also designs where the outer ring is directly shaped into the shape of the motor end cover, which is called an end cover bearing.
3. The gyro frame support requires minimal friction torque to reduce the drift rate of navigation. In addition to the use of ordinary radial ball bearings, a variety of approved structures have been developed. The outer ring has a straight-rolling radial ball bearing, which has a much smaller friction torque, but cannot be axially positioned; a three-ring bearing, the middle ring is driven by a gear. In continuous operation, the steel ball rolls along the raceway, and the starting friction torque is replaced by the motion friction torque, and the navigation accuracy is significantly improved.
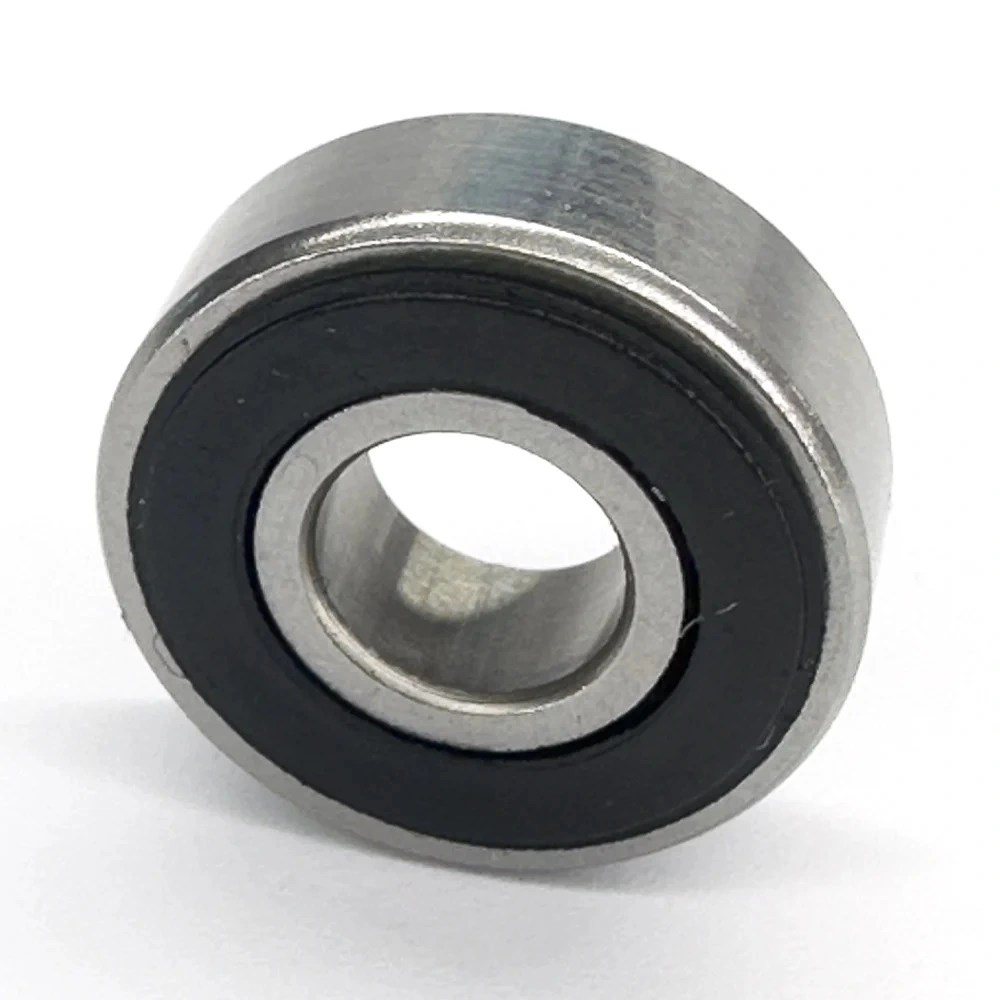
MR148 2RS Bearing
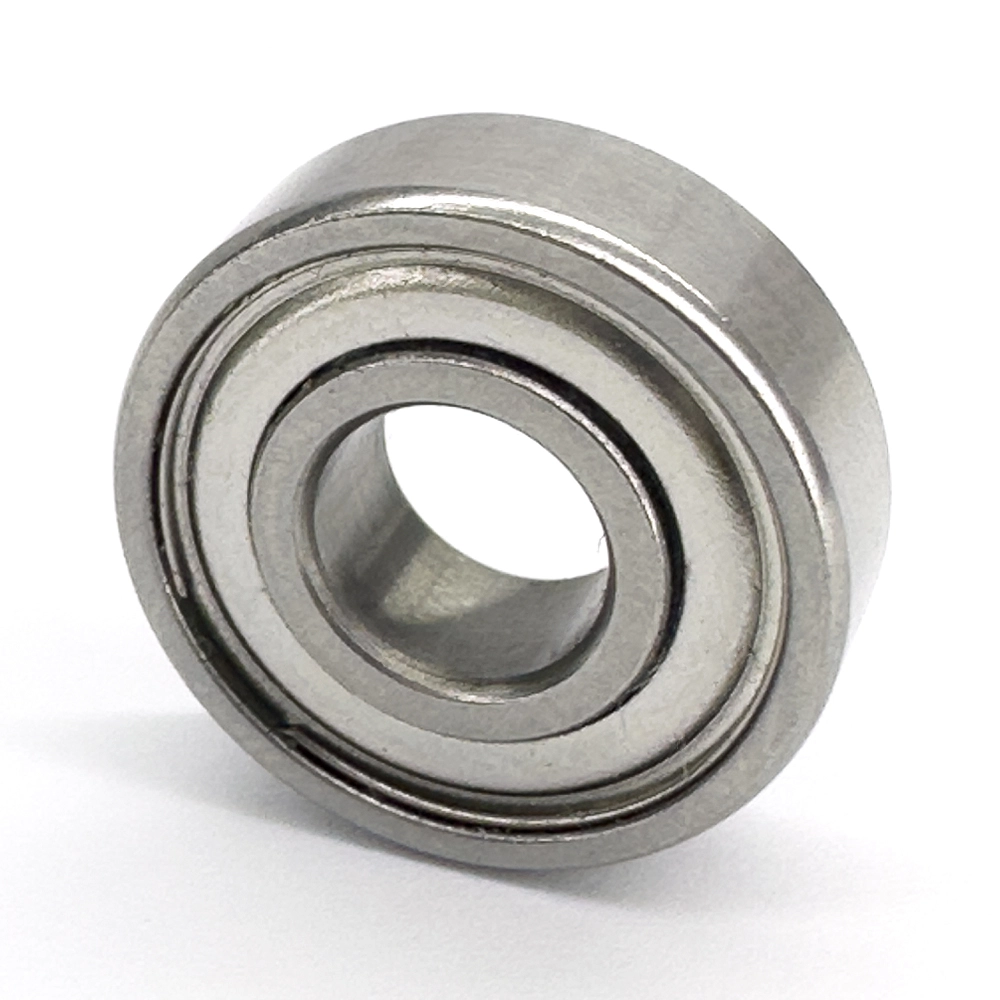
MR148 ZZ Bearing
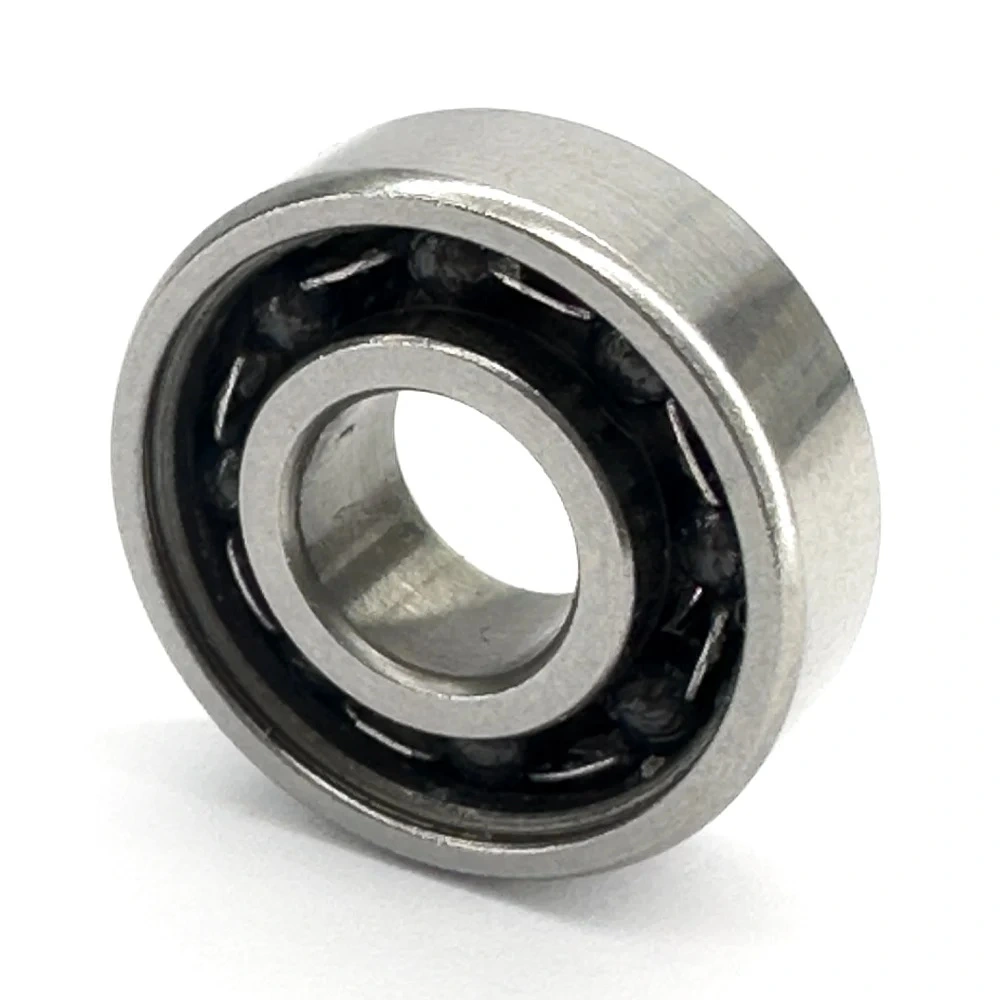
MR148 Bearing
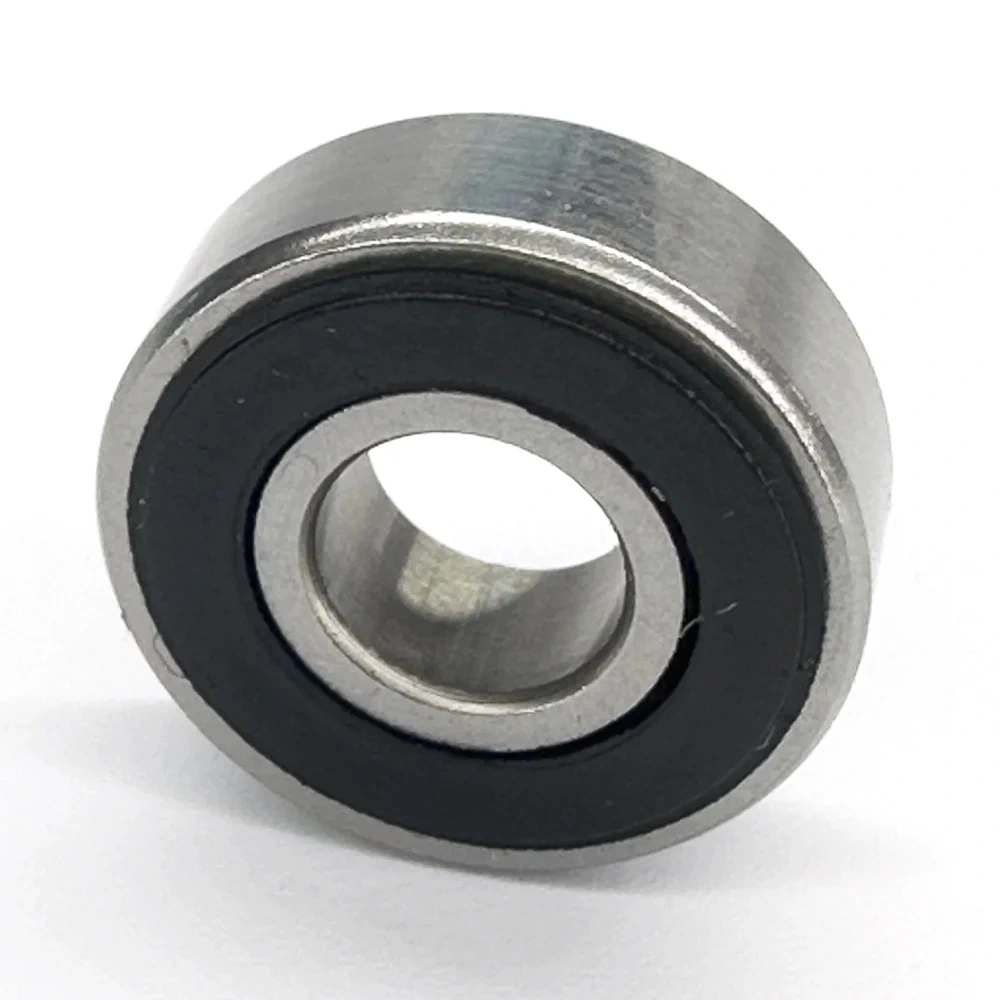
MR137 2RS Bearing
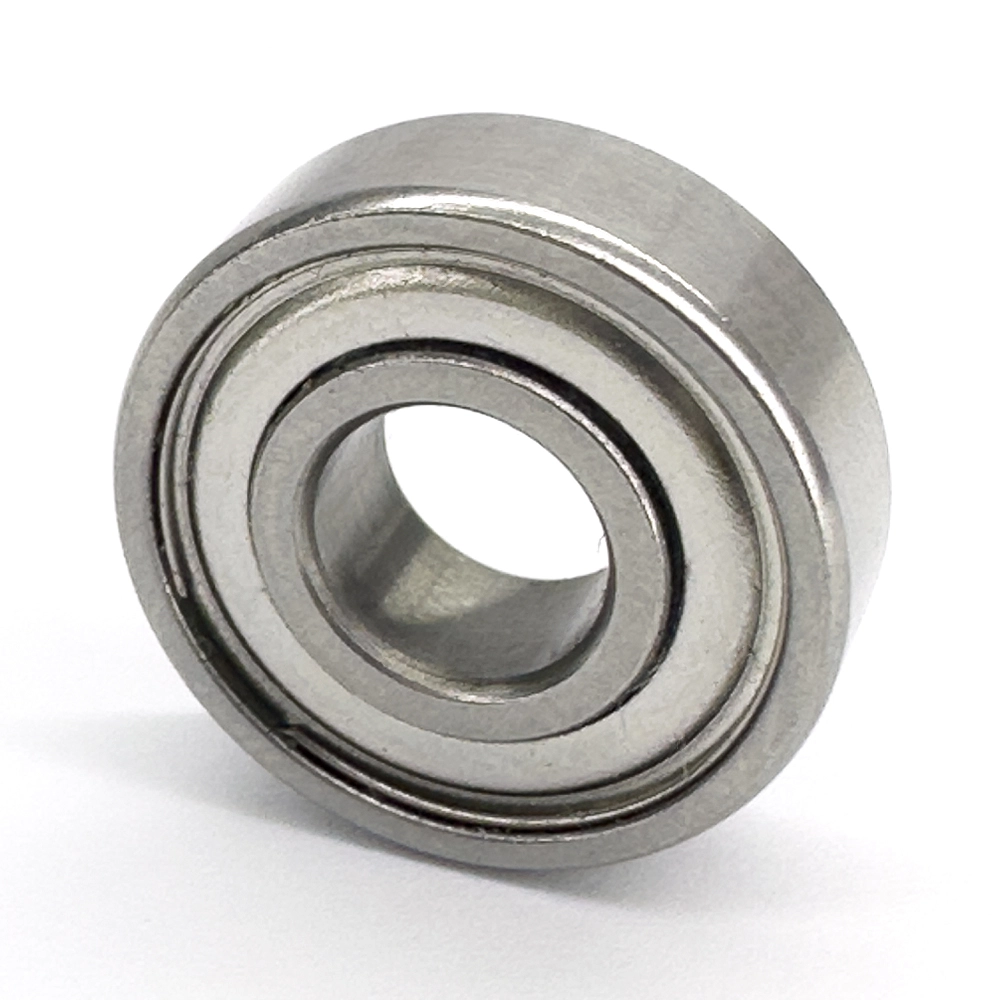
MR137 ZZ Bearing
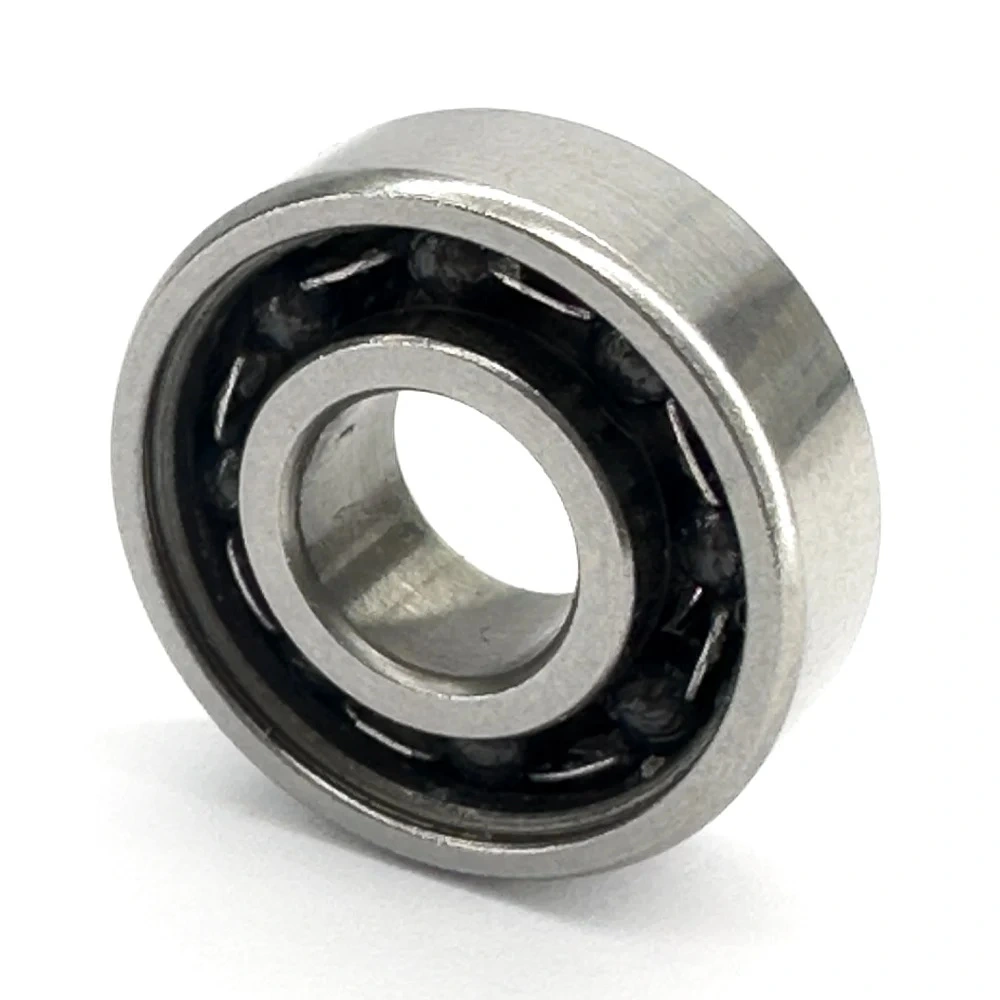
MR137 Bearing
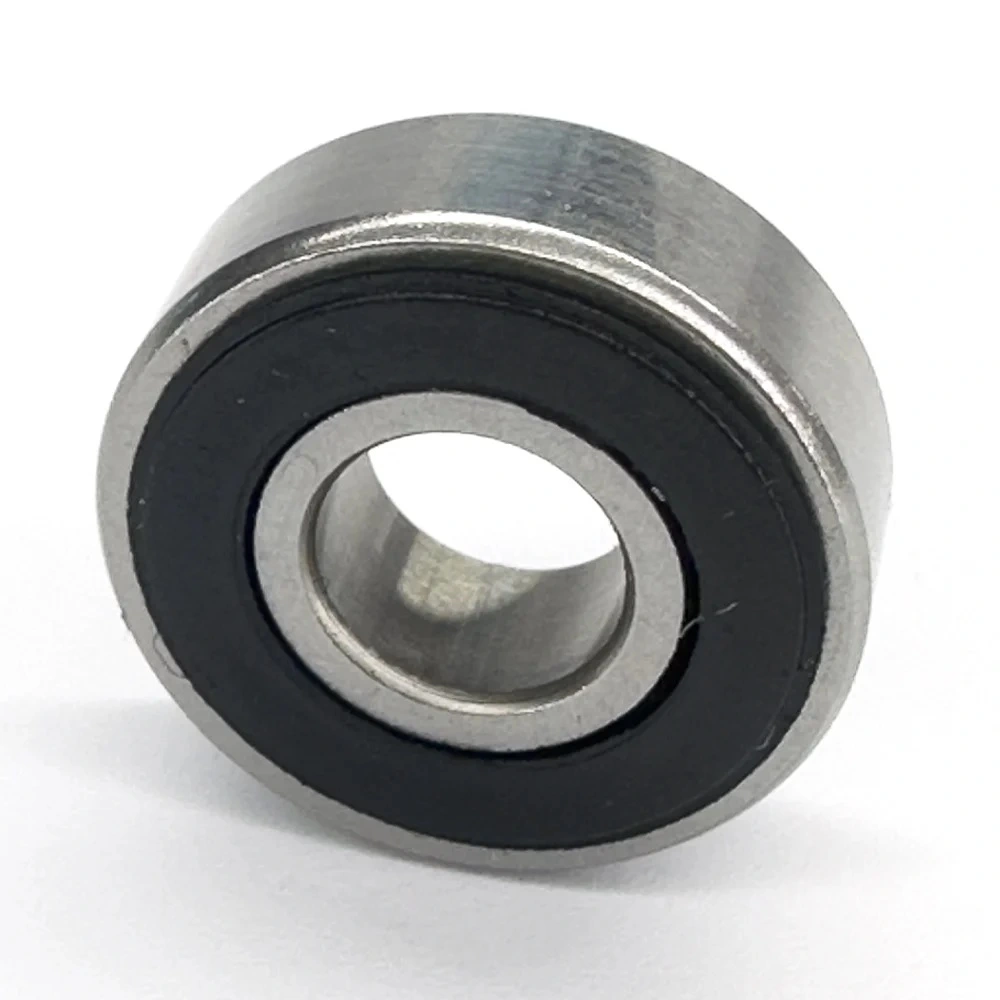
MR128 2RS Bearing
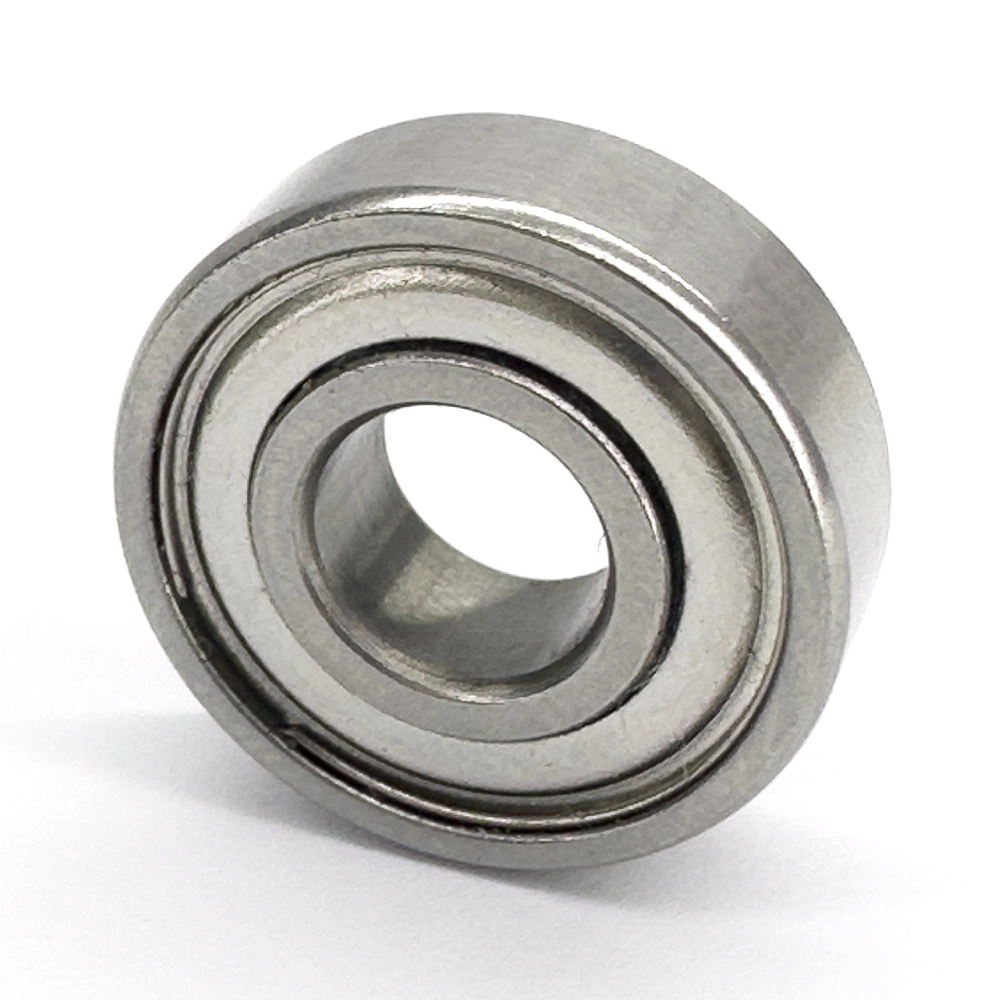
MR128 ZZ Bearing
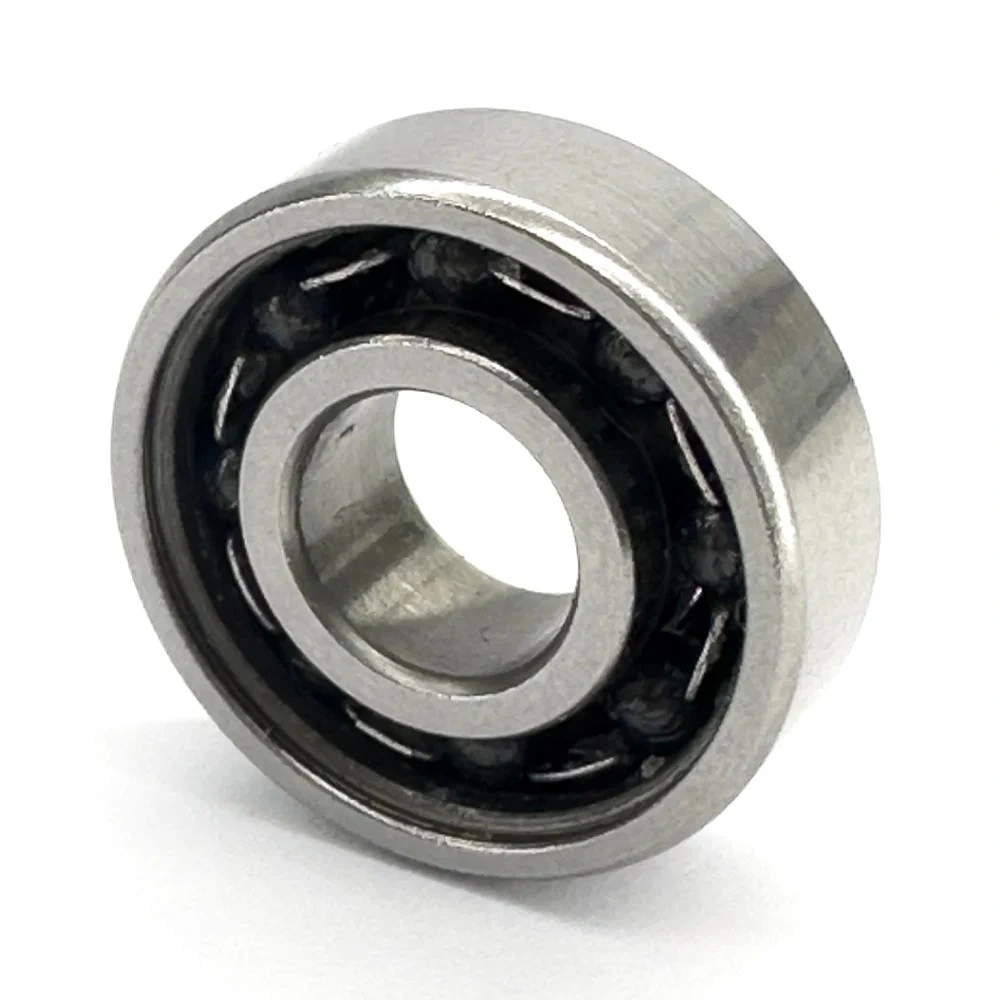
MR128 Bearing
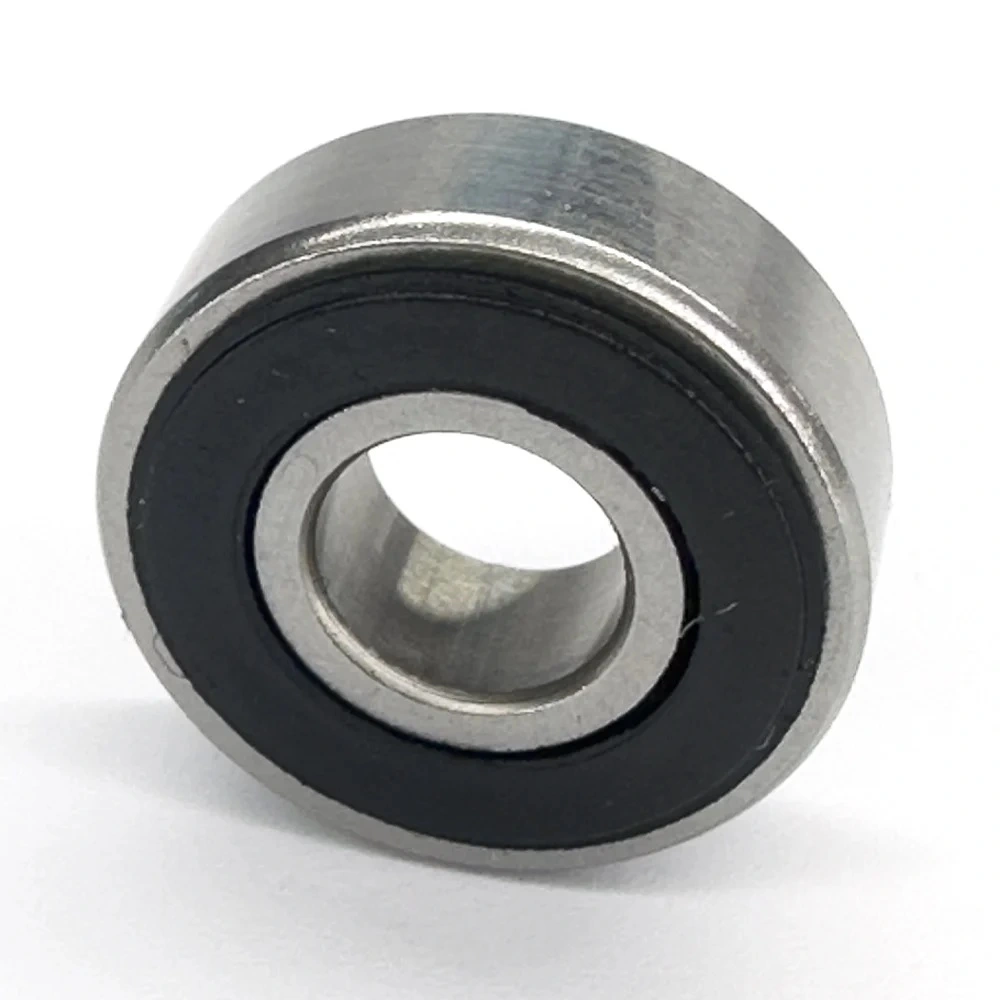
MR126 2RS Bearing
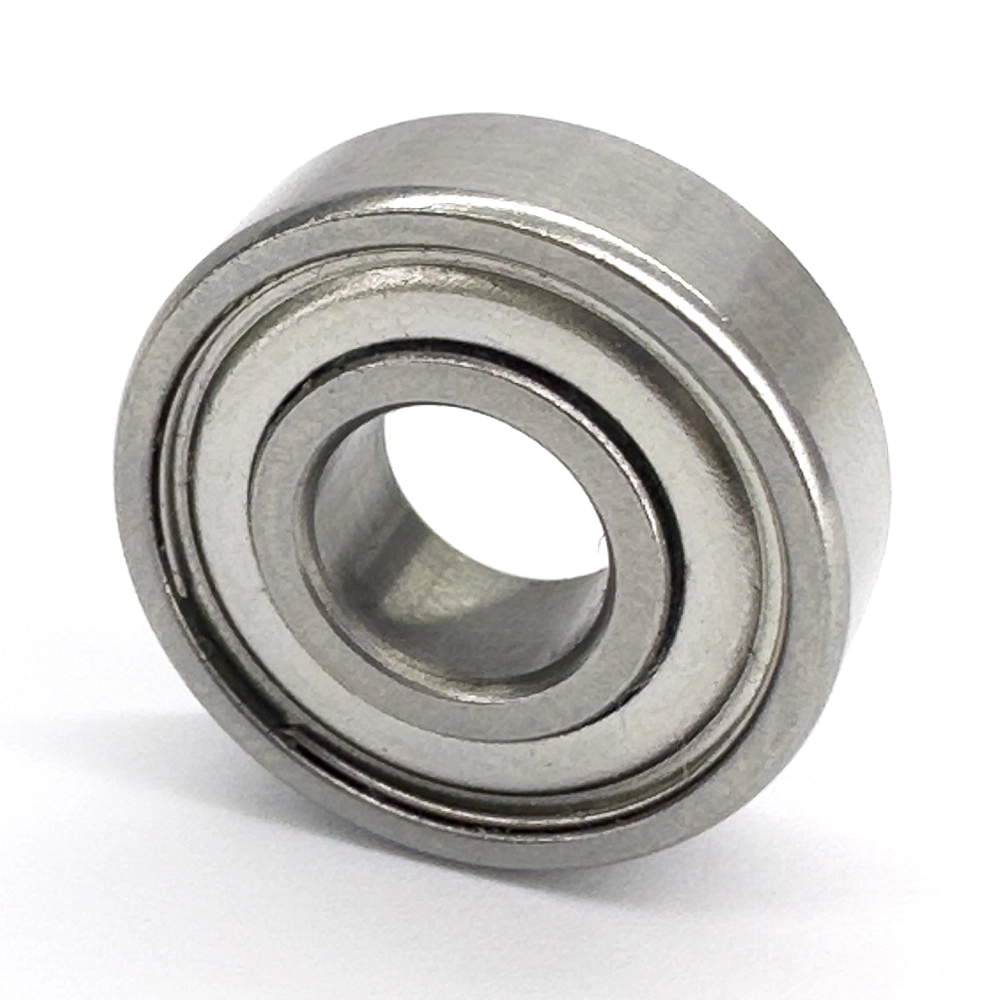
MR126 ZZ Bearing
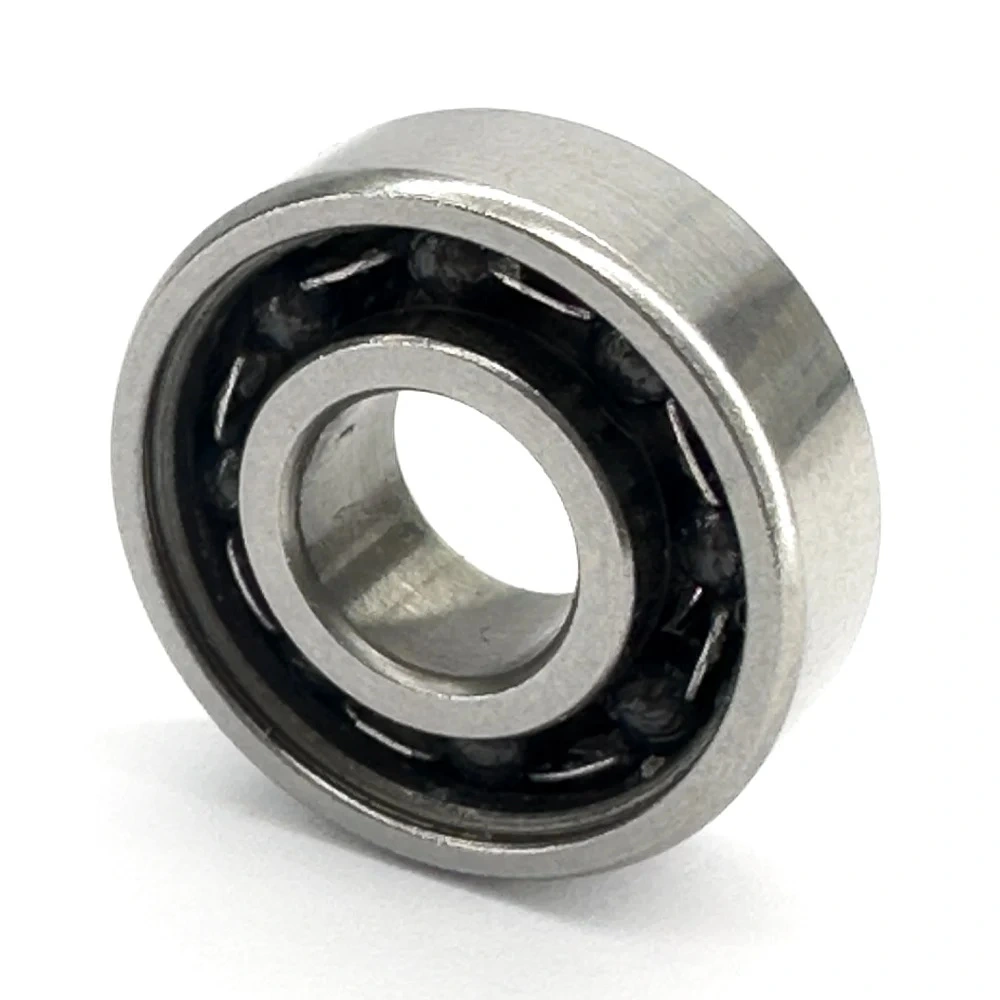